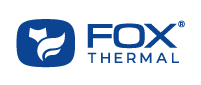
In an industrial setting, controlling processes with accurate data is an essential part of keeping the process running smoothly. Control systems are equipped with instrumentation like thermal flow meters to feed flow data like gas temperature and gas flow rate into the system. So, what is flow rate and why is it important? The flow rate of the gas tells the system how much of a gas is flowing through a cross section of a pipe at a prescribed unit of time. Flow rate data can help with many things, including the following:
Flow meter manufacturers generally list the flow accuracy specification as “% of reading” and “% of full scale (FS)”. To understand these two specs, we have a graph that shows percentage error in relation to the meter’s flow range.
You’ll see that the % of reading and % of full scale give a more detailed look at how the flow meter will perform.
Repeatability of a flow meter is the ability of the flow meter to produce the same results reliably.
In a fully developed flow profile, the gas flow becomes parabolic wherein the gas particles in contact with the pipe’s surface are slowed due to friction and gas particles in the center of the pipe move more quickly. When there is an obstruction or elbow in the pipe, the flow profile is disturbed and forms an irregular profile.
There are installation considerations in the field that can affect how well the flow meter will perform.
First, flow may behave differently in vertical pipes than in horizontal pipes. In a vertical pipe, especially at very low flow rates, gases may swirl or deviate from the ideal center line measurement point that create measurement error.
Also, flow meters installed in pipes that are exposed to extreme temperatures or partial sunlight may also have a degree of error from the varying temperatures. Some flow meter technologies, like thermal mass flow meters do not need temperature or pressure compensation.
A final consideration is the length of straight pipe before and after the installation point of the flow meter. Most manufacturers will recommend the minimum straight pipe runs necessary to ensure the accuracy of the flow meter. When a flow meter is installed too close to an obstruction or elbow in the pipe, irregular flow profiles or turbulence will be created at the measurement point and measurement error will add to measurement uncertainty.
When a new flow meter is pulled from the box, reputable manufacturers supply customers with a calibration certificate that states the conditions under which the flow meter was calibrated, ensures that the flow meter has the accuracy specifications promised, and specifies if the calibration was performed with NIST-traceable standards. This information should be reviewed to verify that the flow meter has been calibrated according to your process conditions, as ordered.
Calibration drift is a common phenomenon that can occur over long periods of flow meter use. When a flow meter’s calibration drifts, it no longer performs according to the original calibration accuracy specs and there is a change in the level of error associated with flow meter readings.
To combat calibration drift, some manufacturers recommend that flow meters must be recalibrated after a specified period and will issue a new calibration certificate upon completion. Some manufacturers offer ways to verify the continued accuracy of the flow meter in the field. Fox Thermal offers CAL-V™ calibration validation that – when performed with the FT View™ software in the field – will produce a certificate recording the results of the verification test in the field and ensures that the flow meter retains its NIST-traceable calibration.
These definitions are given in relation to thermal mass flow measurement.