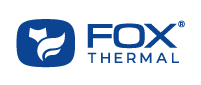
As spring comes with warmer weather, the number of producing wells is expected to reach an all-time high. At the same time, exploration in the Bakken is moving into the upper midwest grasslands which is predicted to further increase this number. Gas producers are looking to measure flare gas, gas from separators, vent gas, and other well site gases with the most accurate flow meter for the job. There are several things to keep in mind when initiating a search for the right technology for these applications.
Gas producers are looking for a cost-effective device to measure the flow of gases at the well site. Thermal mass flow measurement technology most commonly offers direct mass measurement of gases in standard volumetric or mass units with no need for additional pressure or temperature compensation. Thermal mass flow meters are repeatable, offer a broad measurement range, and have a low-pressure drop. Unlike many flow measurement technologies, there are no moving parts with a thermal mass flow meter, and they are easy to install. Most manufacturers offer insertion-type flow meters, remote mounting capabilities, and in-line styles.
The Fox Thermal engineering team has dedicated considerable time developing the most accurate and feature-rich thermal mass flow meters available on the market today.
Most recently, Fox Thermal created a data logger feature with seven-year history that was designed to meet BLM standards for flare gas measurement on federal land leases. The data logger has these advanced features:
In response to calls from operators to verify that their meters were measuring accurately in the field, Fox Thermal developed the revolutionary Calibration Validation feature. This test was the first of its kind to allow the operator to initiate a verification procedure that would not require any additional equipment, canisters or instrumentation. The test is performed in-situ and produces a pass/fail result. When used in conjunction with a free PC-based software tool, it will produce a certificate with recorded data values and a pass/fail result that can be kept on record.
The DDC-Sensor™, a direct digitally controlled sensor, is interfaced directly to the meter's microprocessor for more control, precision, and programmability. This unique sensor design provides a technology platform for calculating accurate gas correlations. The correlation algorithms allow the meter to be calibrated on a single gas in the factory while providing the user the ability to select other gases in the Gas-SelectX® gas menu(s).
Gas-SelectX® was designed to answer the need voiced from many customers that experience changing gas compositions most commonly found in biogas, flare gas, and natural gas flow measurement applications. The menu of available gases in the oil & gas menu offered in Fox Thermal flow meters has proven to be a highly valuable feature in these instances. Tuning gas mixes in 0.1 percent increments to create custom gas mixes “on the fly” has provided the following benefits:
In short, Fox Thermal cares about its customers’ needs and listens to demands in the marketplace. We bring innovative technology that provides solutions to common and complex problems. Contact Fox Thermal today to explore the benefits of this technology further or use the online product configurator to customize a Fox Thermal product for your application needs. Fox Thermal is located at 399 Reservation Road, Marina, CA, 93933. Reach them by phone at (831) 291-4331, by email at sales@foxthermal.com, or online at foxthermal.com/configure.