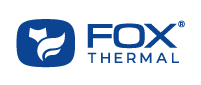
Hydrogen Sources
Although there are many different hydrogen production types including black, pink, turquoise, and yellow, the most common type is from “grey” sources (95%). The steam/methane reforming process is used to convert natural gas or methane into hydrogen. A pollutant by-product of this process is CO2.
There are two emerging methods for hydrogen production: “blue” and “green”. Like grey sources, blue hydrogen is produced from natural gas, but it is paired with carbon capture to mitigate the CO2 emissions. The energy industry is looking at retrofitting current oil and gas infrastructure to make way for blue hydrogen production and transmission. The goal is to reduce overall transition costs by repurposing current equipment and pipelines for the hydrogen and carbon dioxide it produces. For new infrastructure, the goal is to create cleaner facilities with green processes that have no pollutant by-products. Green hydrogen is produced from water through electrolysis using renewable energy sources. Forecasted production using green and blue hydrogen sources is projected to grow faster than other sources.
The Move to Green Hydrogen for Net-Zero Goals
Environmental, social, and political challenges have put pressure on producers to come up with cleaner solutions for our global energy needs and to reach net-zero goals. One solution gaining more traction is the conversion to hydrogen from fossil fuels - or the addition of hydrogen used as a blend with traditional fossil fuels - to fuel equipment and for power generation. During the transition to hydrogen, it is expected that blends with fossil fuels like natural gas or methane will be used. As more hydrogen becomes available and the costs go down, the ratio of hydrogen to methane will rise. For this reason, the Power industry is focused on using equipment that will be able to utilize a full spectrum of blends over time.
Some pioneering investors are moving into creating H-class (hydrogen-ready) equipment and facilities to be first to the market with tested solutions. There are several pilot project sites that are examining this methodology by implementing designs of H-class plants and equipment. Through real-time tests and trial-and-error challenges, these pilot projects are paving the way for future sites to utilize proven H-class equipment and operational processes with less uncertainty about costs, logistics, and existing regulatory/code frameworks.
Where Hydrogen is Being Used Today
The US hydrogen market shows that, of the 11.4m metric tons of hydrogen consumed annually, the largest consumers are refining (57%) and ammonia/methanol production (38%), with steelmaking (2%) and other industries (4%) in the minority of consumption. Other industries are expected to begin or increase use of hydrogen in their industrial processes along with the projected increase in hydrogen use in the Power industry. Accurate flow measurement solutions, like thermal mass flow meters, are key to efficient process control for hydrogen, air, natural gas, oxygen, and other gas flow used in hydrogen applications.
Steam/Methane Reforming – A Grey or Blue Hydrogen Process?
In this endothermic process, high temperature steam and pressure cause a reaction to produce hydrogen, carbon monoxide, and carbon dioxide. These gases are then isolated in a water-gas shift reaction. Steam/methane reforming is a grey hydrogen source and results in CO2 emissions. When the emissions are isolated and injected underground, the steam/methane reforming process shifts from a grey to a blue hydrogen process. The methane or natural gas fed into the reforming process along with the resulting emissions can all be monitored for efficiency or emissions reporting with a thermal mass flow meter.
Turbo Turbine Generator Cooling
Hydrogen-cooled turbo generators use gaseous hydrogen as a coolant because of the low density and high thermal conductivity properties of the gas. Hydrogen-cooled generators are preferred in some applications over air-cooled generators due to the lower cost and size. As more hydrogen becomes available in the market, the use of hydrogen-cooled generators may increase concurrently. Thermal mass flow meters are a trusted measurement solution for pure hydrogen used to cool turbine generators.
Oxygen and Hydrogen from Electrolyzers – A Green Hydrogen Process
With green hydrogen production expected to rise, plant efficiency managers will be under more pressure to optimize their processes to increase production. At the core of this process is electrolysis using renewable energy and water as the input and Electrolyzer equipment units to separate the O2 from the H2 in the water molecules. The welcome output of this process is the oxygen that can either be safely released back to the atmosphere as a non-harmful by-product of the process, or it can be captured and stored to supply other industrial processes. The hydrogen gas produced in this process can be stored as either a compressed gas or liquefied. Electrolyzers optimized with flow measurement devices to monitor both oxygen and hydrogen outputs during the production process will help plant efficiency managers monitor the process for reporting and efficiency improvements.
Flow Meters for Hydrogen Monitoring
One of the most effective techniques for improving efficiency is a precise control strategy. The accurate, repeatable measurement of gases with thermal mass flow meters can help you achieve your performance goals.
In addition to the primary benefits of direct measurement of mass flow rate, low-flow sensitivity, and fast response, the meter’s no-moving parts design also helps reduce maintenance costs. Thermal mass flow meters are easy to install, cost-effective, and are available in a variety of styles to match your installation requirements.
Gas-SelectX® – The Key to a Smooth Hydrogen Transition
The transition to hydrogen will require flow measurement devices that allow operators the flexibility to monitor changing gas compositions used to fuel this new generation of H-class equipment. Gas-SelectX® is a feature that allows the user to choose from a list of gases to create a custom gas mix specifically for their process. The gas menus have a suite of gases that can be mixed in 0.1% increments. The menus are accessible using the configuration panel in the flow meter electronics housing or by connecting a laptop/PC with a USB cable to program the gas mix using a free software tool: FT View™. The flow meter must not be removed from the installation point and the process flow does not need to be stopped while using the Gas-SelectX® feature to re-program the gas composition mix. Gas-SelectX® is available on models FT1, FT4A, and FT4X from Fox Thermal and will play a critical role in allowing operators to keep their flow devices in service even when the hydrogen-to-methane ratio changes over time.
Check out our New Website Application Resources!
Fox Thermal has released this new hydrogen gas webpage to expand our online resources for website visitors.
As hydrogen use increases, this page will serve as a central resource for you and your team to access information and literature impacting flow measurement solutions in hydrogen flow applications.
Visit the new Hydrogen Applications page on the Fox website by clicking here: https://www.foxthermal.com/applications/hydrogen-gas.php
If you’d like to get a copy of our new Hydrogen Application Guide, you can find a copy here: https://www.foxthermal.com/literature/pdf/guides/hydrogen.pdf
If you're ready to get a hydrogen gas flow meter, get started with our online product selector tool here: Help Me Choose