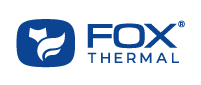
Industrial air compressors and industrial air compressor systems help to convert electrical to mechanical energy to drive countless applications in mining, construction, processing, and manufacturing, but low compressor efficiency makes this a relatively expensive form of power.
Here, we take a closer look at some important tools for improving air compressor efficiency, including the use of thermal flow meters.
Compressed air is widely used to power mechanical processes in all types of industry, but, while powerful and reliable, it is relatively inefficient compared to other types of energy.
Put simply, air compressors require a lot of energy to store a relatively small amount of energy – and that’s a serious concern.
You will find an air compressor of some kind in almost every manufacturing or processing business. While there are many different types of air compressors, they all work to store energy by squeezing air into a smaller space, while also wasting increasing amounts of energy through heat and friction.
It is estimated that 80-90% of the energy used to compress air is converted to heat and that an air compressor can require 4-8 units of electrical energy to produce one unit of potential mechanical energy.
Reducing the amount of energy needed to power air compressors means improved productivity and potentially huge savings on many companies’ electricity bills, but it also includes benefits including:
Lower energy consumption
Less excess heat and noise
Lower maintenance costs and longer machine life
While advances like variable speed compressors make producing compressed air more efficient, the Department of Energy estimates that efficiency in industrial compressed air systems is as low as 10%. That’s why it’s important to treat compression systems as a whole when seeking to improve efficiency.
Here are six ways to improve efficiency and reduce waste across your industrial air compression system:
Most compressed air systems use more pressure than required, leading to increased losses through leaks and heat and more wear and tear on components. Many 100 psi systems will run optionally at 80 psi or lower. Experts estimate a 10% reduction in pressure can lead to a 5% saving in energy costs, over a typical year.
The relative inefficiency of compressed air as an energy source means that even a small leak can waste a lot of energy and put your compressor under significantly increased strain. In fact, 20-30% of your compressor’s output could easily be lost to leaks, and one study found that just a 1/8-inch hole in a 100 psi system could cost a company up to $1,200 a year!
Flow meters are a critical tool for identifying leaks. On large industrial air compressor systems, flow meters provide accurate, actionable information about the efficiency of different parts of your system and the most likely location of leaks.
Performing regular, scheduled air compressor maintenance is the simplest and most effective way to improve system efficiency. All air compression equipment is potentially vulnerable to:
Air pollutants, like dust, dirt, smoke particles, and pollen can build up on parts.
Humidity or water vapor that condenses inside your compressor can cause rust.
Heat buildup means air drawn into your compressor requires more energy to compress, reducing your unit’s efficiency.
A good maintenance schedule will include:
Changing dirty oil and fuel filters
Checking and changing the oil
Draining tank condensates
Cleaning intake valves
Tightening bolts, checking connections, and inspecting hoses
Industrial air compressors are designed to deliver a particular volume of air at a set pressure. Maintaining constant pressure across a large compressed air system can be challenging. Local low-pressure spots, or pressure drops, reduce overall efficiency and increase wear and tear on equipment. Pressure drops are caused by:
Increased local friction with the walls of the pipe or narrowing of the pipe
Leaks in the pipe
Obstructions inside the pipes including sensors, probes, and controls
You can minimize pressure drop by:
Straightening and shortening pipes between source and powered equipment
Making sure pipes are signed for maximum, not average system flow
Installing low-drop controls and meters to minimize flow disruption
Spreading the load by installing two or more smaller compressors or extra storage tanks
Most of the energy wasted by air compression systems is lost to heat and associated humidity. You can improve efficiency significantly by:
Cooling and drying compressor intake air
Shading compressors or relocating them to cooler areas
Investing in a heat recovery system
If you can’t measure it, you can’t manage it. Effective flow metering equipment helps reduce operating costs by ensuring you get the most out of your air compressors and controls. Effective flow metering equipment will allow you to:
Lower system pressure while managing demand spikes
Trace and monitor leaks
Identify and manage local pressure drops
Monitor compressor performance
Optimize controls
Installing modern thermal mass flow meters like Fox Thermal’s DDC-Sensor™ powered flow measurement devices at key points on your compression systems provides a non-stop source of flow and temperature information with negligible pressure drop, providing:
Real-time information on the overall system efficiency
Accurate, repeatable measurements over time
Primary flow meters can be used to verify supply side performance. If the system is not performing as expected, maintenance may be needed.
Flow meters can also be used to locate and quantify leads using submetering on the demand side.
Fox is revolutionizing thermal mass flow measurement technology with:
Award-winning digital sensor (DDC-Sensor™) technology
Microprocessor-based, field-rangeable electronics
Direct mass flow measurement of air in standard volumetric or mass units
No additional pressure or temperature compensation required
Low pressure drop
Up to 1000: 1 measurement rangeability
Talk to us about how our versatile, minimally invasive measurement equipment can help you get more out of your air compression system, or click below to learn how our thermal gas flow meters compare with other in-pipe measurement options.